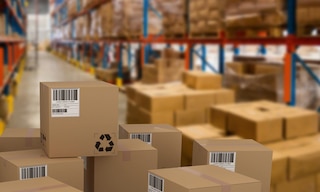
15 síntomas de un depósito desordenado (y cómo resolverlos)
Un depósito desordenado es la principal causa de una logística improductiva e ineficiente. La falta de orden en una instalación logística reduce la eficiencia de las operativas y aumenta el riesgo de accidentes, tanto para los operarios como para la mercadería y los sistemas de almacenamiento.
En este artículo nos adentramos en los 15 principales síntomas de un depósito desordenado y planteamos soluciones para evitar que estos limiten la competitividad de tu compañía.
Depósito desordenado: principales señales
1) Mal diseño del layout del depósito. Puede ocurrir que el depósito no tenga una configuración adecuada para la realidad de la empresa o que no contemple el futuro crecimiento del depósito y la necesidad de adaptarse a posibles cambios en la planificación logística de la organización. El diseño del layout del depósito debe ser lo suficientemente flexible para adaptarse a estos cambios, por ejemplo, destinando más zonas a la preparación de pedidos o contemplando una posible ampliación de los muelles de carga.
2) Falta de aprovechamiento de la superficie de almacenamiento. El depósito debe estar equipado con un sistema de almacenamiento que dé cabida a todos los productos y que aproveche al máximo la superficie disponible. Este sistema, además, debe adaptarse a las características de la mercadería. Por ejemplo, si se gestiona un gran número de pallets de cada referencia, lo idóneo sería implementar un sistema de almacenamiento por compactación (como el Pallet Shuttle).
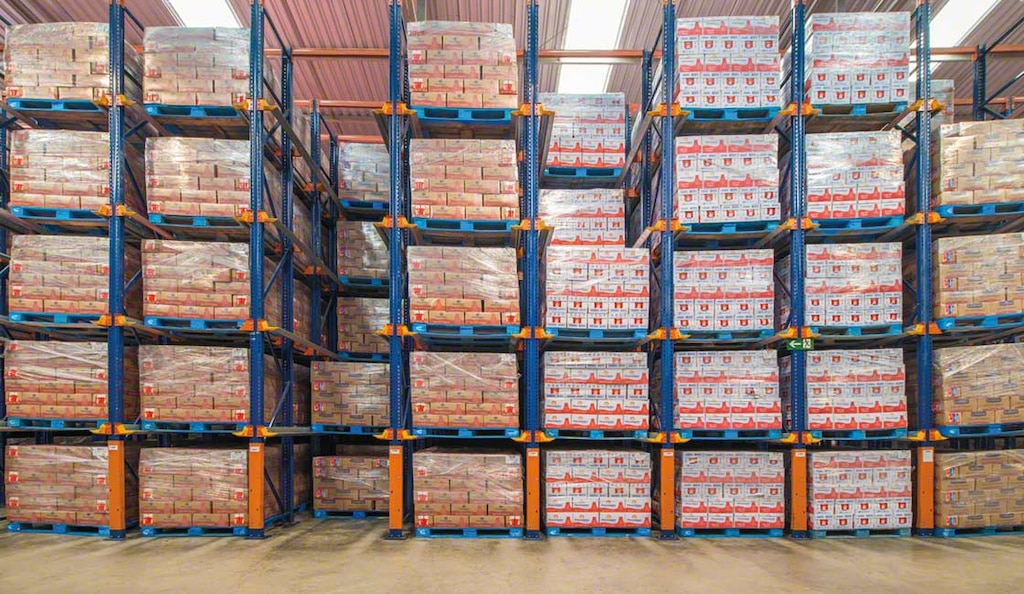
3) Excesivos recorridos de los operarios. En un depósito desordenado, los movimientos de los operarios no están coordinados ni optimizados, lo que les obliga a moverse excesivamente para ejecutar cualquier tarea como, por ejemplo, almacenar la mercadería o completar un pedido. Para resolverlo, es recomendable recurrir a un sistema de gestión de depósitos WMS, que envía instrucciones a los operarios sobre cómo realizar cualquier operativa, indicando con precisión la ubicación a la que dirigirse. Este programa genera la ruta más rápida para que los operarios recorran las mínimas distancias.
4) Desajustes en el volumen de trabajo de los operarios. Una mala distribución de las tareas por parte del jefe de depósito puede provocar desequilibrios en el volumen de trabajo entre los diferentes operarios y la creación de cuellos de botella. Para solucionar esta ineficiencia es necesaria una planificación logística acorde a los objetivos estratégicos de la empresa. Además, módulos del Easy WMS, el sistema de Mecalux, como Supply Chain Analytics o Labor Management System son capaces de monitorizar la actividad en cada parte del depósito con el fin de identificar si existe algún desequilibrio en la instalación.
5) Descontrol en los procesos de recepción y expedición. La existencia de un búfer temporal con sobrestock o cuellos de botella en el muelle de carga son síntomas muy habituales de un depósito desordenado. Estos errores pueden subsanarse con una buena planificación logística que contemple y regule cuáles son los flujos de mercadería dentro de la instalación, cómo se asignan los muelles de carga y descarga y qué papel se destina a la playa del depósito.
6) Descoordinación con las líneas de producción. Un depósito cercano a las líneas de producción ejerce habitualmente como pulmón de producción, almacenando temporalmente las materias primas hasta que se necesitan para cumplir las órdenes de producción. La falta de coordinación podría producir desequilibrios en el proceso de abastecimiento de producción, entregando las materias primas con retraso y errores. Digitalizar este proceso de abastecimiento con un manufacturing execution system (MES) o con un software SGA para Producción es la solución para garantizar que la producción opere ininterrumpidamente sin errores.
7) Fallas en la asignación de rotación de producto. La rotación de existencias hace referencia al número de veces que necesita ser repuesto el stock del depósito en un periodo de tiempo concreto, usualmente un año. En un depósito desordenado es muy complicado hacer un seguimiento de todas las referencias, si bien es algo indispensable para poder planificar correctamente el layout. Con un sistema de gestión de depósitos se puede definir la rotación de la mercadería para evaluar la capacidad de almacenaje necesaria, los flujos de entradas y salidas, así como la planificación de la actividad general del depósito.
8) Roturas de stock habituales. En un depósito desordenado es muy complicado conocer de qué artículos se dispone y cuáles no están en stock. Como consecuencia, puede producirse una rotura de stock, es decir, falta de existencias para dar cumplimiento a los pedidos vigentes, lo que provoca retrasos en las entregas de los pedidos. Una forma de resolver esta problemática es contando con stock de seguridad, es decir, inventario extra para hacer frente a imprevistos relacionados con los cambios en la demanda o retrasos de los proveedores.
9) Sobrestock. Sin un control preciso de los productos, pueden almacenarse más artículos de los estrictamente necesarios para atender a los clientes, superando así a la demanda. El sobrestock presenta un gran inconveniente: incrementa los costos de almacenamiento y la posibilidad de cometer errores. Para que esto no suceda, es recomendable efectuar un análisis predictivo con el fin de calcular la cantidad de artículos necesaria y mejorar la planificación de la demanda.
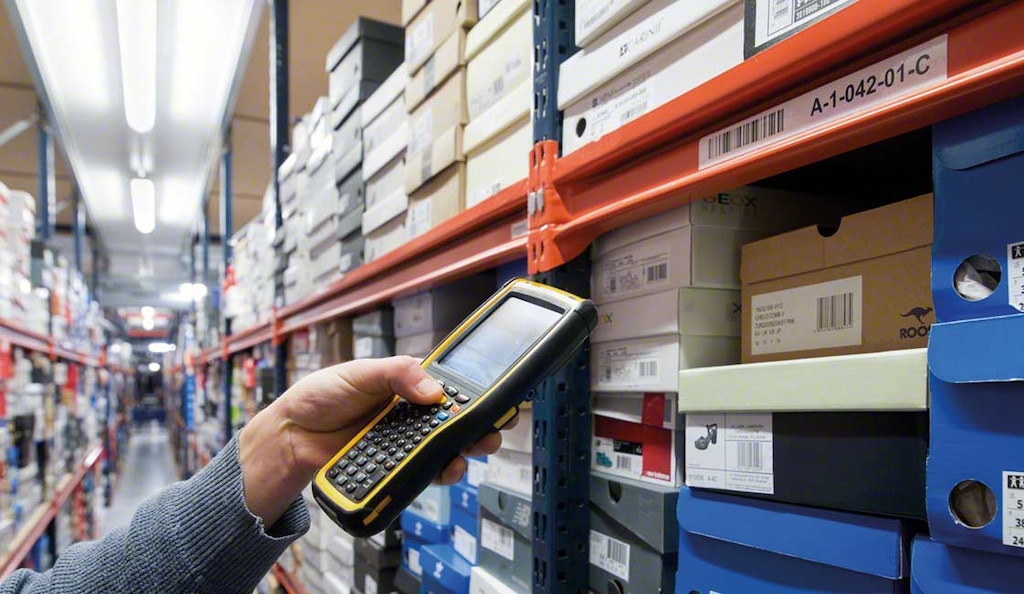
10) Pérdidas de stock. En un depósito desordenado no acostumbran a existir áreas ni ubicaciones asignadas a los productos (o no se respetan debido al caos producido por la falta de orden). Si la empresa desconoce con qué productos cuenta, algunos de ellos pueden permanecer almacenados durante un tiempo excesivo y quedarse obsoletos (no pueden venderse ni entregarse a los clientes). Para evitar pérdidas de stock, es recomendable digitalizar la gestión del inventario mediante un sistema de gestión de depósitos. Esta tecnología permite conocer con exactitud los productos almacenados y organizar la preparación de pedidos teniendo en cuenta el stock disponible.
11) Inventario fantasma. El inventario fantasma se refiere a los descuadres entre las existencias en la tienda o el depósito y el stock registrado en un programa de inventario. En un depósito desordenado, es habitual cometer errores en la gestión del stock, como por ejemplo organizar la preparación de un pedido sin que el producto se encuentre físicamente en el depósito. Para evitarlo, lo idóneo es hacer un inventario periódico, que permite comprobar si las existencias en el sistema y en el depósito coinciden, o un inventario permanente con la ayuda de un WMS.
12) Picking ineficiente. La preparación de pedidos es una de las etapas más costosas para la logística de un depósito. Por ese motivo, hay que asegurarse de que el método de picking escogido simplifique las tareas de los operarios, garantizando el cumplimiento eficiente de los pedidos y evitando los errores derivados de la gestión manual. Implementar un programa de gestión de depósitos o apostar por dispositivos de asistencia al picking, como el pick-to-light o el picking por voz, pueden ser las mejores opciones para conseguir una preparación de pedidos eficiente.
13) Fallas en la preparación de pedidos. Los errores derivados de la gestión manual del proceso de picking comportan un incremento de la tasa de devoluciones. Organizar la logística inversa es un quebradero de cabeza para muchas compañías, además de suponer un sobrecosto operativo que puede menguar su competitividad. Por este motivo, es importante que se limiten los errores en la preparación y expedición de los pedidos. Un WMS simplifica las tareas de los operarios, indicándoles paso por paso las operativas que deben realizar. Esto es especialmente importante en el proceso de devolución de pedidos, donde el software automatiza la reubicación del producto en la estantería o en otro pedido, minimizando los costos.
14) Descoordinación con carriers y operadores logísticos. El proceso de expedición y envío de mercadería ha de ser ágil y eficiente para cumplir con las condiciones de entrega acordadas previamente con el cliente. La falta de coordinación entre el depósito y los diferentes partners en estos procesos puede dar al traste una gestión eficiente del pedido dentro del depósito. Por este motivo, es indispensable comunicarse con las agencias de reparto mediante un sistema de gestión de depósito s que garantice la completa visibilidad del stock durante cualquier fase logística. Para minimizar los errores en la entrega de pedidos también existen módulos específicos, como el Multi Carrier Shipping Software de Easy WMS, que se coordinan con el programa informático del carrier, automatizando el proceso de expedición y generando automáticamente las etiquetas necesarias para el correcto envío del producto.
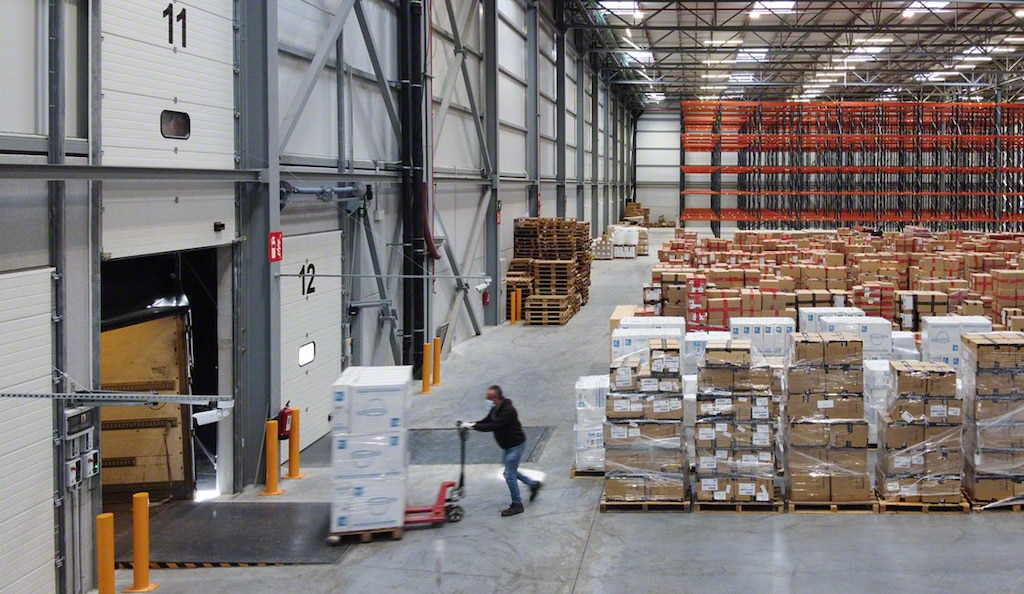
15) Alta incidencia de accidentes. El desorden dificulta las tareas de los operarios y aumenta el riesgo de golpear los diferentes elementos del depósito (otros operarios, la mercadería o las estanterías). Con una señalización del depósito adecuada, los operarios pueden identificar zonas mediante paneles con colores y formas geométricas, evitando así posibles riesgos. También debe realizarse periódicamente una Inspección Técnica de Estanterías (ITE) para verificar el buen estado de los sistemas de almacenamiento y asegurar el funcionamiento seguro del depósito.
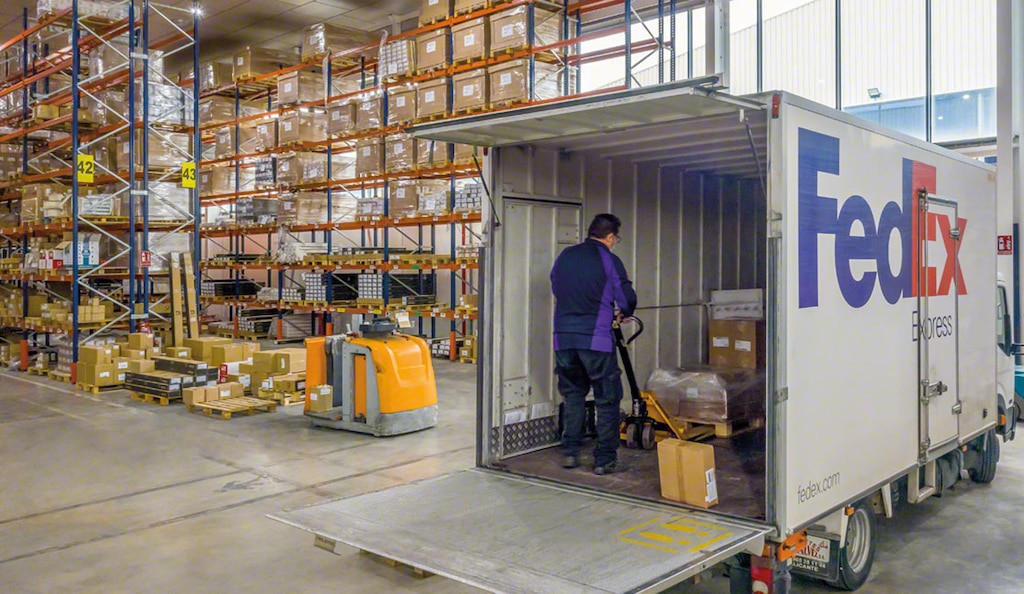
Depósito desordenado: punto crítico en la planificación logística
Un depósito desordenado conlleva graves problemas estructurales para la logística de una compañía. El caos organizativo o la mala gestión del stock y de las expediciones, por ejemplo, lastran la eficiencia de los procesos, reducen el margen de beneficios y perjudican la reputación de cualquier empresa. Identificar a tiempo los síntomas que conducen a estos escenarios resulta fundamental para implementar las soluciones necesarias y restablecer unas condiciones operativas óptimas.
Si detectas en tu depósito alguna de las señales repasadas en este artículo, una buena solución es consultar a un proveedor global de soluciones de intralogística como Mecalux. Contacta con nosotros y un experto consultor te asesorará en la mejor propuesta para la logística de tu empresa.