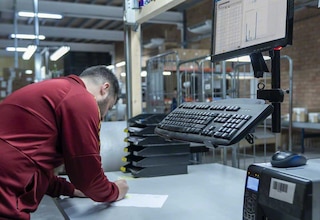
La mejora continua y su aplicación en logística
La mejora continua tiene como objetivo aumentar la calidad y el rendimiento de un producto o un proceso a través del análisis constante de los elementos que intervienen. Esta técnica, de origen japonés, es cada vez más popular entre las compañías occidentales. La mejora continua promete una mayor eficiencia en la empresa gracias a cambios pequeños, pero continuos, que buscan la eliminación de dinámicas improductivas y la estandarización de reglas.
En este artículo analizamos en qué consiste la mejora continua, cuáles son las principales estrategias y cómo podemos aplicarla al sector logístico.
¿Qué es la mejora continua?
Las técnicas de mejora continua son un conjunto de estrategias que tienen como objetivo perfeccionar y optimizar procedimientos, productos o servicios mediante pequeños ajustes como resultado del conocimiento profundo de las operativas y el análisis de datos.
Existen múltiples métodos que aplican la estrategia de mejora continua para potenciar el rendimiento de una instalación. No obstante, el método Kaizen o 5S se ha convertido en uno de los más populares debido a su simplicidad y efectividad.
La mejora continua a través del Kaizen
El Kaizen (“el cambio para mejorar”, en japonés) es un sistema que desarrolló el ingeniero nipón Taiichi Ohno para el fabricante automovilístico Toyota tras el final de la Segunda Guerra Mundial. Su función era incrementar la competitividad de la empresa y equipararla con la de las compañías estadounidenses. Sin embargo, hoy en día se ha convertido en todo un estándar en la gestión empresarial de compañías de todo el mundo.
El método Kaizen parte de la premisa de que, aunque un proceso cumpla correctamente con su cometido, siempre hay un margen de mejora. Aplicado especialmente en los ámbitos de producción y logística, esta estrategia se sirve de un conjunto de procedimientos para analizar el funcionamiento empresarial, detectar ineficiencias e implantar cambios. Todo gira alrededor de cinco principios, conocidos como las 5S por su nombres original en japonés:
- Seire (Clasificar): el primer proceso del método Kaizen consiste en cribar las tareas para discernir cuáles son las que aportan un verdadero valor al producto o servicio (las denominadas gemba).
- Seiton (Ordenar): el trabajador debe tener a su alcance todas las herramientas útiles para ser ágil y productivo. Aplicar Seiton consiste en organizar los equipos de trabajo para evitar desplazamientos o movimientos poco eficientes.
- Seiso (Limpiar): la identificación de fallas y la limpieza del lugar de trabajo son claves para que el operario se sienta cómodo y trabaje a su máximo rendimiento.
- Seiketsu (Estandarizar): tras la identificación de las fallas, se establecerán las reglas o estándares necesarios para aumentar la eficiencia de los procesos.
- Shitsuke (Disciplina): esta última etapa es fundamental para el éxito de las cuatro anteriores. Implica el compromiso por parte de toda la organización de interiorizar las nuevas reglas y adoptar una filosofía de mejora continua para incrementar el valor de todas las operaciones que se desarrollan en la compañía.
En definitiva, a través de las 5S, el método Kaizen es una estrategia ideal para incrementar la rentabilidad de la organización, identificar y eliminar todas las ineficiencias y, sobre todo, potenciar todo aquello que aporte valor.
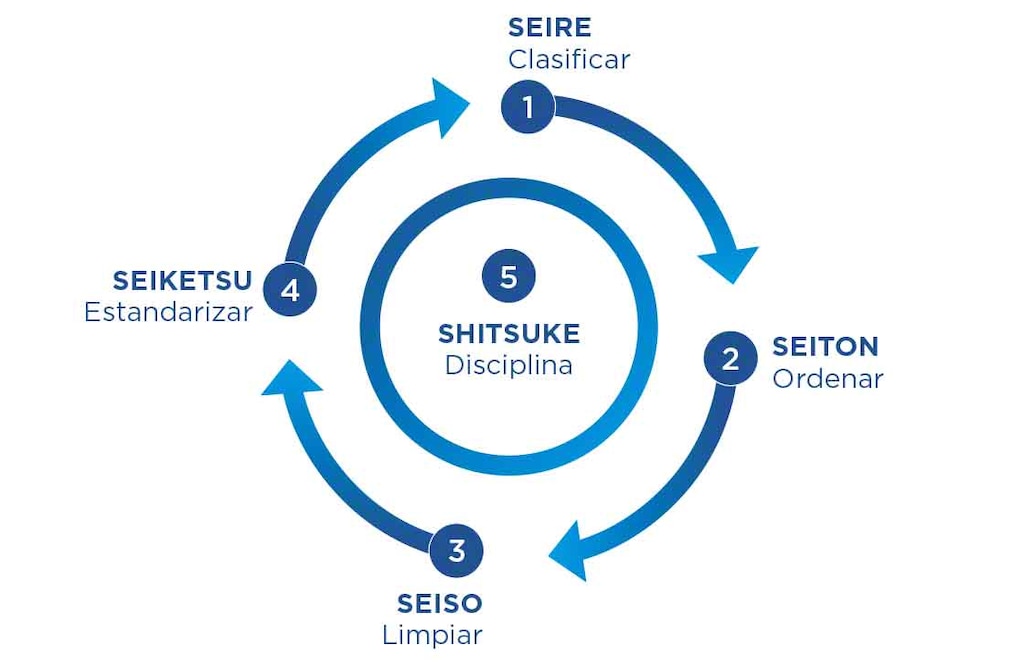
Otros métodos de mejora continua: del PDCA al Six Sigma
Además del método 5S, existen otras estrategias o herramientas aplicables a la mejora continua. Su prioridad es lograr la excelencia en los procesos a través de la información que se genera. Estos son otros dos importantes métodos para la estandarización de la mejora continua:
- El Ciclo de Deming o PDCA: PDCA es el acrónimo inglés de ‘Plan, Do, Check, Act’. Esta estrategia cíclica describe los cuatro pasos esenciales para detectar ineficiencias, planificar soluciones y, a la postre, mejorar la rentabilidad de todos los procesos que se realizan en el depósito.
- Six Sigma: esta técnica de mejora continua consiste en la supresión de errores en la entrega del producto final al cliente. El objetivo de esta estrategia es llegar a un máximo de 3,4 errores por cada millón de oportunidades, entendiendo por errores cualquier incidencia que impida que el cliente quede satisfecho.
- Metodología Lean: la estrategia Lean se basa en localizar todas aquellas etapas que no proporcionan un valor añadido al producto final, para poder obtener así un producto de la máxima calidad.
Para llevar a cabo la mejora continua no hay que elegir entre un método u otro. No hay uno que sea mejor que otro. Son complementarios entre ellos y cada uno ofrece unas ventajas. Todas las estrategias pueden y deberían aplicarse a la vez. El objetivo es siempre mejorar: reducir ineficiencias, introducir cambios incrementales y asegurar la correcta adopción de los nuevos hábitos en toda la empresa.
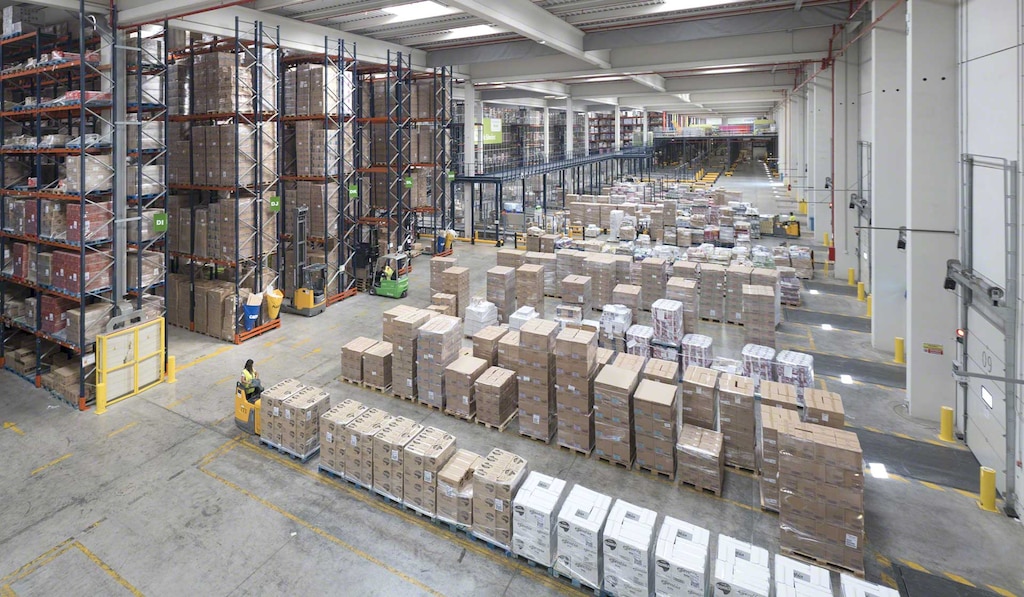
El desperdicio: muda, mura, muri
Las técnicas de mejora continua incorporan el análisis continuo de procesos para asegurar la máxima rentabilidad en cada etapa. Por ejemplo, los términos muda, mura y muri engloban una estrategia para identificar errores y despilfarros en la producción.
Este sistema, también conocido como las 3M del Sistema de Producción Toyota, se basa en analizar los errores y desperdicios de un proceso productivo para, mediante cambios en la organización, producir sin fallas y garantizar la mejor experiencia para el cliente final. Estos son los tres conceptos clave:
- Muda (despilfarro): se conoce como muda aquellos errores que consumen recursos y no agregan valor añadido al producto final. Originalmente, el método de Toyota integraba 7 desperdicios que ocurren usualmente en un centro de producción: movimientos innecesarios, excesos de inventario, reprocesos (operativas repetitivas), sobreproducción, tiempos muertos entre líneas de producción, sobreprocesos (procedimientos que no aportan valor) y transportes poco eficientes.
- Mura (irregularidad): el responsable de producción debe hallar cualquier desequilibrio, interrupción o alteración en la carga de trabajo que provoque un sobrecosto en las líneas de producción. Para ello es imprescindible un control exhaustivo sobre el rendimiento de los procesos de producción, con el fin de identificar defectos, errores o incumplimiento. ¿Cómo resolver estas irregularidades? Implantando metodologías que alineen la producción con la demanda, como por ejemplo Kanban o just-in-time.
- Muri (sobrecarga): un conjunto de muda y mura (despilfarros y defectos) provoca lo que los japoneses atribuyen a muri, es decir, estrés. Una mala planificación provoca cansancio en los operarios o, incluso, cuellos de botella en las líneas de producción.
En definitiva, aplicando paso por paso el método de las 3M de Toyota, se suprimen los despilfarros en la producción y las alteraciones y desequilibrios en la carga de trabajo. Todo ello, la eliminación de muda y mura, redundará en la erradicación de muri, es decir, del estrés e inestabilidad en las líneas de producción.
Beneficios de implantar la mejora continua en un depósito
¿Cómo puede ayudar la mejora continua en la actividad logística y en el día a día del depósito? Estos son los principales beneficios:
- Garantía de un producto/servicio de calidad: implantar una técnica de mejora continua asegura el éxito en fases como la producción o la logística, lo que conlleva una mejor experiencia para el cliente final.
- Reducción de costos logísticos: esta estrategia posibilita disponer del número de existencias óptimo en un depósito, disminuir el lead time de los proveedores, priorizar las operativas más productivas y suprimir aquellas que no proporcionan valor.
- Movimientos eficientes: métodos como Kaizen o PDCA eliminan desplazamientos innecesarios y proponen rutas de picking más eficientes, garantizando una mayor productividad para los operarios.
Además de estas mejoras, la implantación de estos sistemas facilita la incorporación de una mentalidad pull flow en las instalaciones. ¿Qué significa esto? Que los procedimientos del depósito operen bajo JIT (just-in-time), es decir, que las tareas se ejecuten cuando exista una demanda del cliente final, evitando operaciones poco eficientes y riesgos como el sobrestock o que la mercadería quede obsoleta.
En ese sentido, Mecalux dispone de múltiples soluciones para apoyar la implantación de un método de mejora continua como Kaizen o PDCA. Supply Chain Analytics Software, la funcionalidad avanzada de Easy WMS, permite al responsable de logística recopilar todos los datos del depósito y estructurar esa información con el fin de determinar los KPI logísticos relevantes y medir el impacto de la estrategia de mejora continua.

Mejora continua como garantía de competitividad
En un contexto logístico en eterno cambio, con tecnologías que están llamadas a revolucionar el día a día de las empresas en un futuro no muy lejano, las empresas deben ser capaces de introducir mejoras continuamente y así mantenerse competitivas.
El primer paso hacia la eficiencia en la cadena de suministro es monitorizar y analizar los KPI del depósito con el objetivo de identificar deficiencias y prescindir de aquellos procesos que no aporten valor añadido. Implementar una estrategia de mejora continua en la empresa es el único camino hacia la reducción de costos logísticos y la optimización de los recursos de que dispone cada compañía.
Si quieres maximizar el rendimiento de tu depósito, no dudes en contactar con nosotros, un consultor experto te ayudará a sacar el máximo beneficio a la logística de tu organización.